The Smartest Linear Motor Wire Cut EDM? Let’s See Why CHMER Users Think So! | High Precision
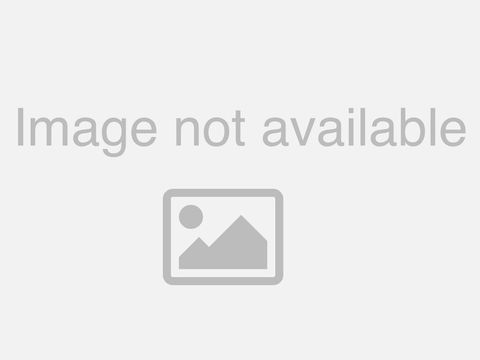
Welcome to CHMER, I am Brad Wang, the General Manager here at CHMER. Today I will be giving you overview of who we are and what amazing product we can offer. Let’s get started with outline of this remarkable company. CHMER was founded in 1975 to produce Die Sinker EDM for the mold making industry. We are a machine tool company and have been operating for 45 years.
Our original focus was on building cutting-edge EDM machines by 1980, CHMER was the leader of EDM in Taiwanese market since then. In the early 1990s, we expended operation building three factories one after another in China to have a higher productivity. In 2009, we moved to the latest headquarter, that sit on an area of total 28,000 meter square, for the purpose of global operation and R&D center. Up to this day, CHMER is the fifth-largest EDM manufacturer in the world. At the heart of our Business Philosophy is Integrity, Growth, Customer Satisfaction and Employee Security. We like to think the business philosophy is the cornerstone of our operation here.
With this concept in mind, we gain confidence and motivate ourselves toward success. CHMER obtained 42 national awards over the past decade. This truly recognizes CHMER’s commitment to bring awesome experience exceeding our customers’ expectations. The list of a wide range of national awards includes the outstanding management performance, technological innovation and good design of product etc.
We believe that without the hard work and dedication of our employees, there is no way CHMER would be such successful. The original product line consisted of Sinker, Wire Cut and Drilling EDM. Afterward the High Speed Machine was produced. Since 2018, we developed a more holistic approach, the newest products, Laser Cutting Machine and the Electrochemical Machine were released over this time. Technology is the core of CHMER. We have a staff of 40 working in our R&D division.
There are four teams here, specializing in mechanical, electrical, Mechatronics and software design. Our R&D team accounts for 15 percent of the employees in CHMER. Generally speaking, we devote 5% of our revenue to the R&D efforts and this number may even increase.
To this day, we continue to place an emphasis on research and development activities to create over 50 patents. Indeed it is their innovation that drives our company forward and sets us apart. Let’s move to the next production line. Take a look, this bright, spacious, air-conditioned production area makes the building a very pleasant workplace.
It’s also perfect for assembly of high-accuracy machines and superb product assurance. Additionally, it is so neat and tidy thanks to lean system that has been maintained by our great teams. We also implement a CPS manufacturing system. CPS can produce machines efficiently with Top-quality and shorter delivery that fully satisfy all customers’ requirements. Quality delivered is the No. 1 driver for a firm’s success.
The final stage, testing is where the product is examined to weed out any defects. Our quality control inspects carefully and does not overlook any important detail on our product. It is a critical part of the process since anything less than 100% quality guarantee will damage our reputation.
Hi everyone~ welcome to CHMER In the area of large mold manufacture, What kind of machine will be suitable for customer? Let’s listen to the customers need : The machine is too big cannot fit in the factory; Hope the machine accuracy will be good enough to use for long term. Can we have a popular machine appearance? Can we have stable AWT to less the wire threading time and less the cost for consumable? All your need are heard by CHMER professional R&D! 16 new patents in new generation of RV series will fix those problems in 1 time. The new generation of RV series brings customers with aesthetic design and gives machine the sense of elegance. Also embedded with 19 inches touch screen control panel. and LED work Light for the operator , all ergonomic designs will make your work easier.
To achieve the goal of no backlash, high accuracy and high reliability, CHMER in-house linear motor drive system can do it for you. Compared with ball screw drive, The maintenance is more easier with longer life span CHMER in-house linear motor drive system is your best choice. High energy-efficiency water system. it is a smart water recirculation device. with the partitioned tank for the sedimentation and circulation. This stabilize the water quality and reduce turbidity of the work tank And gives you extra 50% longer life of filter, and use less consumable.
IWA (Intelligent Working Aid) including 4 functions combined with intelligent manufacturing automation to improve the processing efficiency. High speed water supply and outlet function. The real time control of water supply and outlet save 1/3 time than the previous generation. Automatic water replenishment function With the intelligent sensing detection, the water valve will automatically open and add water when it is less in the water tank. The intelligent liquid-level control system the function saves time 5-10mins of pre-processing each time especially they are different cutting heights in one process. Programmable sliding door The function provides with the best safety and achieves automated process.
It can follow the liquid level and stop at any point to save time for loading and unloading. The most of fast and stable AWT system Nearly 100% success threading rate attains unmanned operation. Threading in the break point or under water, it is no need to return to the start point and waste time in draining and refilling water. Free setting the threading mode according to the cutting condition for the continuous machining with the threading assistant device, Threading for high thickness workpiece is not longer troublesome.
We have to say this is the most of stable AWT system in the world. The standard is set up! Through certifications of patents on RV series to perfection, we successful fulfill the customer’s need for the large mold. All the function is not only deal with the problem but also is the standard for new generation machines. We do welcome everyone to have the wonderful experience with us! Our RV series is not only designed with great appearance and highly rigid structure, but requires smart controls and a strong heart to show its perfect performance.
RV series wire cut EDM is equipped with the all new i8 +power supply. The new power cabinet has a modular PCB design, which is easy to assemble and maintain. With a DC fan to enhance the cooling performance, It can maintain a stable machine temperature at high-speeds for continuous production without PCB problems. For consistent machining accuracy a stable power supply is vital.
We build our own smart AVR power supply that uses a newly developed IVC(Intelligent voltage control) high frequency switching power supply. It provides ripple Voltage bellow 300mV and conversion efficiency above 90%. The unstable external power can be changed to high precise internal power for higher accurate machining. Innovative discharge circuit design. The discharge circuit for processing energy control transistor uses the high-current type IGBT module design. Compared with the MOSFET type before, IGBT reduces the thermal effects and transistor numbers, to save the cost in the future maintenance.
Compared with the resistor used before to consume the heat and waste the energy, The ineffective energy is now directly reused while machining. The i8+ power supply not only saves 20% of energy but also reduces indoor heat generation, This provides a stable working temperature for machining accuracy and saving energy in one time. We have the latest anti-wire break function. It estimates the thickness of the workpiece and changes the cutting data in time. The combination of software and hardware works when there is a step difference in processing to improve the machining efficiency. Setting different sparking wave forms with the processing conditions can increase the cutting efficiency on thick parts.
CHMER fully self-developed controller shows our own impressive R&D capabilities and give the commitment of after service to users. The controller includes many functions such as: 1.Pre-loaded with 50 sets of copper wire parameter selection. 2.Intelligent programming allows users to quickly start the production. 3.3999 hole data makes the multi-hole information more complete. Teaching newcomers is easier with less technical gap by our UI (User Interface) conversational operations.
Our professional R&D team provides the strongest development capabilities to customize the software and hardware for customer’s jobs. Anyone is familiar with CHMER previous products or new users can feel a significant increase in cutting speed. The new i8+ power is like the Engine of an Automobile, and how valiant of this engine? Let's go to see how it does.
Comparing to the previous G7 power supply, we can obviously to see the difference on old & new structure. With the new i8+ power supply, WIith The work conditions on a HRC55 SKD-11 steel @50mm thickness, we can opportunity to see the cutting speed stability varied from 160mm2/min up to 180mm2/min It’s a 12% efficiency improvement if compare to the G7 power supply. Same work conditions when we are doing @ 100mm thickness, we see cutting speed stability varied from 105mm2/min up to 120mm2/min, It’s a higher efficiency improvement about 15% efficiency if compare to the old G7 power supply. It’s an incredible experience to work on a high thickness Job.
We would say ''YES'' on new RV & i8+power the best match. On the RV wire cut we could get the result an excellent 3~5µm accuracy along with a good 0.55~0.65µmRa surface roughness on a thickness 30~100mm Job.
It’s almost the same to work on small size wire cut machine. Even we look at 100mm~200mm Job. it’s still a good cutting accuracy in 10um(micron meter) and just slightly reduced @0.6~0.65umRa surface roughness. Awesome.
And the most surprising thing when doing at thickness 200~400mm job , we can take a 15~19um accuracy ; just a little pity the surface roughness will down to 1.9~2.4umRa, however, It’s not bad for users actually. Let’s take a look how the reduction of outer profile error, especially from line to arc segment in NC programming path. A perfect cutting demo because the combination of hardware (linear motor plus i8+ power) and software (W5F Operation System) A smooth machining path, a small radius angle error which is perfectly be controlled in 1~2um accuracy, With a free and easy operating that we have almost forgotten RV is a giant size machine. Amazing user' experience.
We have a conclusion about radius corner error being well controlled in 3um. Just like driving a 4 wheelers (4WD) PICK-UP, which overcomes all difficult NC programming paths, what a pleasure cutting experience to operator, isn't it? We could see more proves from the cutting demons. An excellent cutting result in 3µm accuracy and surface roughness by 0.46µmRa. Another sample we could see overall features likes as (high thickness/high accuracy /high cutting speed). it’s almost forget it’s not a small wire cut machine, after all, this 'RV' is a Taiwan excellence Gold Medal awarded wire cut machine.
Let’s move it! Try it now! Challenge themselves beyond the limit. The incredible surface roughness 0.46umRa result could happen on a 30~50mm thickness Job.
The user will crush on this RV wire cut, wants to developing how the potential of this RV wire cut does. What are your waiting for? Experience it for yourself. The customers of RV series are mostly from the industries of aerospace, automobile, energy and home appliances. Now let us check the prospects of these industries together, we will know the importance of RV series in the next few years. In the aerospace industry, the global commercial fleet is expected to reach 50,660 airplanes by 2038.
About the region markets, the Asia Pacific region, which includes China, will continue to lead the way in the future growth In the automobile industry, the global electric vehicle market is growing rapidly and it is estimated that the ownership will reach 130 million in the next decade. The total sales of electric vehicles will increase from 2.5 million in 2020 to 31.1 million vehicles in 2030. In terms of the energy industry, IEA sees the offshore wind sector to become $1 trillion industry by 2040 with global capacity set for a 15-fold increase. Regarding the home appliance industry in the next 5 years, the smart home appliance market is predicted to achieve a compound annual growth rate of 16.5%,
reaching 39.63 billion by 2024 With the data from each industry above, furthermore, we have to know the role of RV series in these industries on molds and parts processing. 80% of wire cut are used in mold manufacture including press, progressive die, plastic injection… etc. according to the design for continuous and automated mass production. For example: the oil pan, the transmission of cars, the TFT TV, fridge or air conditioner… in home appliances. Although part processing is only 20% in wire cut use, the application for it is literally no limitation.
Only the workpiece has to be electricity conductive. Of course, the cutting speed and accuracy are different from various materials and required shapes. For instance, the turbo blades in the aerospace industry and the transmission parts of energy industry. Apparently, the market for large size wire cut EDM is wide and huge; CHMER RV series will also lead the way with our customers forward! Today I want to introduce the conception of industrial 4.0 Industry 4.0
is about connecting the digital and physical world today, from vision to implementation. It is how machines are infused with intelligence. For the fourth industrial revolution.
Let's have a closer look at it. What CHMER could do for you and how did we get here. The brand new "remote monitoring and M2M system provides all the information by portable devices when you are offsite. The core technology of the Intelligent Information Center is gathering all the machine data and build the machining history daily, weekly, monthly to create a big database.
This system benefits your business prolong the lifespan of your machines, reduces costs while increasing the production efficiency. How smart is the design, let's go over the details. A factory manager can check out the working status of each machine, such as wire cut EDM and Die sinker EDM. No matter where these machines are, across the world like Vietnam, Thailand They can be checked.
A production operator can set up a programming online, review the temperature of machine, water and environment, diagnose the outer problem and get an idea of lifetime of spare parts. We could analyze the ideal working time in a certain period to increase the efficiency in production. Not only by PC, but we also could download CHMER APP on cell phone and tablet. Even if you're travelling, you have access to all the information that you wanna anytime.
The RV series wire cut EDMs are combined with modern design smart functions and optimized integrations. That is requirements of advance manufacturing. The RV series wire cut EDM bring the user the most amazing experience to connect to the industry 4.0. Brand spirit of CHMER is to build better products for customers to provide an awesome experience beyond their expectations, to create a win-win value between enterprises and customers. Committed to becoming a world-class leading brand in non-traditional processing solutions.
CHMER offers you knowledgeable sales and product information whenever you need it. Our sales people want to hear from you, they want to help you to make the best use of our products. Our 24-hour service and support is unmatched in the industry. We also provide you customized service. Our sales, Technicians and R&D engineers work together to meet your requirement completely. We are trusted for our flexible design capabilities and allow us to provide you accurate, fast and extremely cost-effective solutions.
The accuracy requirement for the mold of press machines is higher than the injection or the forging. If you would like to make a great mold, wire cut edm is playing a key role. When we have some special demands, we will discuss with CHMER for more research and improvements. They always provide us a good response on our requests and replies. The most important thing is that our products are tested and used by customers according to their needs.
CGC technology company only produces very accurate workpieces. The machine is proved to do our jobs, we believe it is absolute good enough for other areas. Moreover, the reason that I have been working with CHMER instead of other brands is because your people are all professionals and the stability is convincing. I believe in CHMER because of their business philosophy and direction, which are going in a very positive way. I believe what I see and what I see is their progress in the professionalism. CHMER products have been sold through global sales network with 90 representations in over 55 countries around the world.
CHMER delivered more than 25000 machines in the past 45 years.
2021-04-27 17:03