Advanced Vision & Dispense Systems Integration Andrews Cooper ATX West 2024
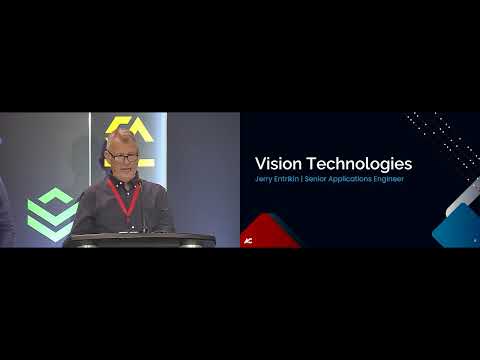
so we're Andrew Cooper we're a endtoend Engineering Services provider and we work through all aspects of the product commercialization so starting out with helping people with R&D into product development into testing Hardware through the automation process and even to service and support at the end so that whole end to end process we can help people whatever position that they need their help in whether it's engineering resources or product development we've got a team that can help in throughout all those areas we're here at ATX because we do sophisticated Precision automation custom automation for people and helping people find solutions to their tough challenges my name is Ryan Harris I'm a application engineer at Addis Cooper and my background is mechanical engineering I've had about 24 years experience in custom automation design and a large portion of that time has been designing systems that have dispensing of one type or another hi and thanks everyone for coming my name is Jerry entri and I'm the senior's senior applications engineer at Andrew Cooper as well my background is automation controls Machine Vision and software development 30 years experience in custom Automation and development at Anders Cooper we've been providing Engineering Services for over 23 years and have become a trusted partner for solving complex engineering challenges for emerging Technologies we work with companies large and small in various areas of Technology including in consumer electronics Medtech space exploration and Warehouse Logistics and Robotics today we want to talk about Precision adhesive dispense and vision Technologies so one of the things that led us to this topic was in the middle of developing an optical system for a large AR VR client that we were working with we found that there was this need to prove some very precise adhesive dispensing and make sure that their whole product could actually be viable and so they weren't sure what type of adhesive to use whether it whether they could do a with adhesive or they'd have to come up with some mechanical means to assemble this Optical system but they needed somebody to help them with that and especially in some of that Precision dispensing to see if they could shrink down the size and put it into a form factor that would be manufacturable and a lot of these techniques in this presentation are geared around that customer and what we did for them and how we solve their problem and really that's what we do we try and help companies you know realize their product development through whether it's the product development side for it's testing helping them design some testing systems for it's helping them do design for automation getting them to that end goal of final Automation and a commercialized product let's start with micro dispensing so now miniaturization really has been important in a lot of different Technologies so Electronics manufacturing we all are familiar with cell phones how everything's been condensed down our cameras on our phones everything that's condensed into our phones and with that comes the need for the miniaturization of manufacturing of assembling all those tiny little components and often times that means dispensing tiny little group amounts of adhesive in precisely the correct place and that goes for medical device fabrication it goes for biomedical even that 3D printing and additive manufacturing they're doing some very small micro printing as well now and then Optical display Technologies again your cell phone camera is a good example of that just shrinking down getting high quality and a very tight small package and dispensing is all part of assembling those very small little projects whether it's that an adhesive or maybe it's an alant or maybe it's some kind of gas getting material whatever you have precise control over your whatever your dispensing is becoming very important so I want to start with just a little reference of scale so what are we talking about when we're talking about like a people leader volume or even a micr leader so I just put up a slide to give you a little bit of idea of what a picol leader means in terms of the diameter of a sphere so if you're looking at say one Peak a liter it's about 12.4 microns in diameter and then if we go over on a reference of scale for our distance then that 30 to 40 Micron range is our heal visibility threshold and then as we move up 100 microns is roughly the size of a human hair and then getting up to 500 microns we've got our table Sal and then a millimeter the thickness of a dime and so then as you can see from when you move to picol to nanoliter to microl you can see that kind of grow too and it gives you at least a little bit of a feel for what we're talking about when we're talking about a nanoliter of fluid dispensed down a pathway it's we're talking about about a human hair of a fluid dispensed down a pathway so one of the key parts of micro dispensing and dispensing of any type is matching the product with the correct technology viscosity is often used to numerically provide someone with an idea of what that fluid is like but there's so many other characteristics whether it's sticky or stringy or gritty or oily those play a very key role in what technology might be used for dispensing that product and there's a lot of different dispensing Technologies out there that have been out there for a long time and some of them have really been getting refined getting better and better more tighter control more precise control and so today to focus on the pzo driven jetting dispensers and then the rotary positive displacement pumps using the endless piston principle and couple of the manufacturers that we've really had success with in some of these Technologies is the bisco tech and nordson they've both got some very good products that I'll touch on here that we've used in some of our applications to be successful in solving our customers challenges so I'll start with this pzo jet non- cont micro dispensing solution non- contct is really key here for this dispenser it allows you to dispense without actually bringing your needle down to the product and following whatever path that might be so typically if you have a a needle dispensing a product it needs to get close enough to the product to where the surface tension of the product can keep it dragging along and we can keep it into position as you're moving it now with the pizo jet you can actually fly above the material and jet that down which is really good when we're talking about some of these very small tolerances because you can imagine if you're dispensing something in that nanoliter range that bead if it's a human hair all of a sudden that surface that you're dispensing on has you have to know exactly where that surface is if you're dispensing down a nanoliter bead of material if you can use a picol leader You Can Fly Above That surface and even if you have a little bit of imperfection in the molding tolerance or your Stack Up tolerance of whatever it is that you're using or manufacturing that then you can compensate you you don't have to be exactly you don't have to map that surface out so to speak and the other nice thing about this technology is it works well for very different types of viscosities of materials even soldering paste they're using this for chip manufacturing and be very precise with where they're placing these droplets the other one that we have used is the visco tech their their rotating displacement pump and this one has been really good for us as well where it it really is a unique way to to create individual precise units of material that you're conveying down a channel and it's different than a typical augur and that an augur moves the whole amount of material this actually pinches off if you will in that lower right corner you can see individual billets of material that are the same volume and what that allows is as you dispense that down you have those individual billets of material that are the same volume and when you you get to the end you can actually generate a lot of pressure right near the tip of where you're dispensing so that gives you really good control right at the tip of where you're dispensing whether you're and even suck Mac like the little video there shows so you can dispense really well you can suck back really well to cut off and you can also meter your material very well through typical encoders and things on your system so uh the visot tech has been able to get down to that 250 Nan range with this technology and it's really been helpful for us in a number of applications and and it works for solid based materials sheer sensitive media it's been good for different sticky materials and that suckback really helps cut off the material on your dispenser so some of the challenges that you face in micro display dispensing applications they're similar to other dispensing applications but often times they're magnified and even with the advancements and refinements of these micro dispensing Technologies there's still many challenges that exist once you try and integrate that solution to automate it so you might be able to get your product dispensing very nice out of one of these Technologies but now we need to integrate that in into a piece of equipment that can put that droplet or that live that you're trying to produce onto the right surface in the right place every time and that's where part-to-part variation can become really critical and the need for other Technologies to make sure that your surfaces are the same or you're mapping your surfaces every time you need to look for is your tip clean because sometimes on these really small applications if you get a little bit of product on your tip and you're trying to dispense that around that can affect that bead as you're laying it down so keeping your nozzle clean making sure you understand your variations in the product that you're manufacturing and even environmental stability is a is an important aspect to consider where vibration can become a big deal sometimes temperature and humidity becomes a big deal down to these levels and then your typical dispense issues so you've got air and traving in the product that can affect your bead size it can create voids in your bead that you're laying down and then dripping cut off lot to Lop product consistency product shelf life those are all things that you know micro dispensing application become more and more critical and things that you really need to look for when you're using this technology so with that I guess I'd like to turn it over to Jerry and he can talk a little bit about some of the vision applications I'm going to attempt to build up to 3D Vision by discussing how we got there and the components that build up to 3D Vision we've used 3D Vision techniques fairly extensively for measuring components and measuring the adhesive beads that we put down on them and also regular 2D Vision but the incorporation of Machine Vision Technologies is an integral part of dispensing systems enables applications that might be difficult or impossible otherwise dispensing very precise quantities requires that you know where going and precisely how it's getting there and how much you're dispensing at Andrew Cooper we have a sense of experience integrating machine vision technology when paired with our motion and dispensing expertise it is the case that there's a lot of really wonderful products here at the show and we're systems integrators so we take the products that you can find here and if you have a product developments that needs a solution we can help you if it's off the shelf we're probably not the right company to go to so if there's something that isn't available off the shelf we can help you with your product development cycle Vision Technologies for precision automation first what is Machine Vision Machine Vision Technologies enable automated machines to detect and interpret their surroundings cameras sensors Imaging processing image processing algorithms allow systems to mimic human Vision perception but only with crater speed and and reliability and accuracy the Machine Vision field is changing very rapidly today not many years ago conventional Vision Vision algorithms were deployed which was basically straight software but today there's a proliferation of machine learning and AI based V Vision processing systems and I'm going to talk about some examples not all in the dispense domain but all of them are pertinent to dispense and that they can be applied there an example I like to bring up is when I first got out of college over 35 years ago in the Machine Vision World binp picking was an ideal that you could have a robot that could reach into a bin of jumbled parts and picked them out accurately and it was a goal of the industry and as recently as five years ago there wasn't practical applications of B picking but today there's another number of companies on the floor that provide products that will allow you to reliably pick coupon from bins with robots so the field is changing rapidly because of software advances we'll start up with how do we get to Machine Vision imagine a point sensor does nothing more than measure the intensity of light at a single location that might be good for determining presence or absence of a part in a system but if I take that point and I move it along a line and clock out that data now I know the intensity of light along a line and maybe that allows me to locate a component in a system along a single Dimension there's many ways to get the higher dimensions of inspection sometimes it's by moving the sensor and sometimes it's by adding more arrays of the sensors a line scan camera is an example of a line of single sensors and so instead instead of moving a sensor we now have a line of sensors maybe a thousand of them and so I can statically pick out a line and I know the intensity along the line and I can use software to active on that now if I want to go to two Dimensions I can take that line sensor and I can move it normal to the line and I'm clocking out an XY image so line cameras are often used for long stripe images when you need to look at a lot of data in a long continuous line you clock the data out of the line As you move it over the component being measured but we can also take an array of lines and put them into a grid and what do we have it's the camera and our cell phone it's a two-dimensional sensor that has pixels in X and Y we can take a single image and we can use that and act upon it with vision processing algorithms to find component location orientation and do Metrology um applications on it example of how you might extend a 2d camera into third three dimensions would be to move that camera through Focus as as we move it through focus and we pick out the regions that are in Focus we can take a 2d camera and by moving it we can establish a 3D profile of the object that's under test additionally 3D Systems can be generated through stereoscopic systems just like human eyes there's a separation of the eyes and we can infer using software from the two images the displacement and determine the depth of the imagees we see and some of the companies like a AI use two cameras and a and an AI based system you give them a model of your product they will then send it into their AI engine jumble it up and they'll come back with a system that can then pick those products from a bin under highly varying light conditions and they can also pick up parts that are transparent where you can see through one part into a part underneath and it's all done with just two cameras it's really quite impressive another technique that we use quite a bit for inspecting adhesive beads is a moving line we determine displacement by having a laser spot or a laser line and we look at it with a camera a 2d camera coming in at a own angle and as we scan that line the apparent location of the line tells us what the Z position is the position of the scan head tells us X and the width of the camera tells us y so we can map out actively 3D surfaces with a moving line another system is to to determine dimensionalities to use structured light here a single camera is used and projected upon the component is structured light typically light bands and dark bands and by using software by analyzing the light and dark bands and how they're affected by the Target you can infer depth information and last but not least our direct arranging systems uh we maybe have all seen these in some of the Prototype self-driving cars around it's a scanning laser beam that rter scans the environment and it measures time of flight of the laser to admitting to the Target and back and so it develops ups at 3D image of the space around it and then Auto automated cars can tell the difference between a pedestrian and a traffic cone and other traffic that might be in the area Vision system processing capabilities I touched on this a second ago but there's two domains that these land in today there's conventional algorithms and there are Ai and machine learning based algorithms conventional algorithms typically use discrete tools like Edge searches areas of Interest template model searching and you build those up into a sequence in order to do a vision inspection these are these have been used for many years and they're very effective but they usually take a highly trained or skilled programmer to put them together uh in some cases the companies that build these have made them very easy to put together like in a graphic manner where you can put together the various locators to find them but typically they require someone who has a certain amount of skill in this Arena the machine based learning systems that are available today however are extremely helpful and they're extremely easy to set up especially if you're looking to determine the difference between a good part and a bad part all it's needed is develop a library of images where you determine these are good parts and a library of images these are bad parts you feed them the machine Learning System it develops its own internal modeling and it will now when it acquires an image it will tell you whether that part is good or bad based on the library of good and part bad parts that it gave to you sometimes Vision systems need to perform critical measurements maybe we want to know the width of an adhesive bead or the diameter of a deposited droplet there are systems available uh today some from keans that allow you to have a a superposition of both machine learning and conventional systems to get the best of both worlds so maybe you use the machine learning portion to find the orientation and the location of a part and then you can apply Edge finders and template searches to establish Metrology information what's the width what's the height what's a critical go no-o measurement for that component decisions that that impact implementation success successful implementation depends on more than just picking a vision system important decisions that you need to make when you're in this domain are how easy as it to set up and maintain if it's hard to set up if it's hard to maintain you'll spend more money you'll spend more time putting that system into operation and keeping it running selection of Optics and illumination depending on what your inspecting you may be able to get away with an inexpensive lens for your camera system but that may be completely inappropriate if you're doing Metrology where you need a more expensive lens so selecting the proper Optics is extremely important and also selecting the proper illumination sources depending on what you're inspecting there are many different types of Illumination that can either make the job harder or easier some targets require coaxial illumination with some targets are best inspected using dark field illumination picking the right illumination Source can make your job much easier when it comes to actually processing those images another component of this that that we like to talk to and where we actively like to be engaged with our customers is in the realm of design for manufacturability often we get a product already designed already set in stone and it turns out that just the addition of some fiducials to allow the Machine Vision system to properly locate that part in space in order to process some of the manufacturing operations could have been added for no cost but we're at the point where we can't add that anymore so it makes the manufacturing side much harder so it's always important to spend some time thinking about the manufacturability of your product patterning is where you're dispensing perhaps microarrays of droplets onto a substrate and uh I guess another way of talking about it I imagine when the pattern completely overlaps people might refer to that as printing so in the same way that a single like sensor can be extrapolated into a line of sensors and an array of sensors a single pizo drop dispenser like Ryan was referring to earlier can be built into an array potentially hundreds or thousands of droplet dispensers in a linear array and then if you move that linear array across the substrate we can effectively print microarrays or we can print other things that are helpful so these are useful for dispensing Biologicals reagents Mass compounds and even conductive substances for literally printing wires and in all of these cases active feedback is really important right it's one thing to have a dispenser that can dispense precise amounts but first you need to be able to lot align your substrate very precisely so having those fiducials to find where the substrate's at precisely on your print platform is very important and fiducials that give you accuracy that are several times greater than the print accuracy that you're trying to accomplish is ideal one example of that would be a chrome on glass standard where you can get submicron accuracy for those fiducials again if you need it but when we're talking about very small deposition sites we need very accurate position additionally these arrays of pazo dispensers require maintenance periodically especially depending on the substance being dispensed and when you first start them up maybe every nozzle isn't printing properly perhaps one's blocked perhaps there's some buildup on the nozzle head and it'll cause a droplet to be skewing off to the side so there needs to be an initial print quality check done and that's best done by Machine Vision so you can verify every droplet is in the correct location and then there's dispense pattern triggering Gazo dispensers eject droplets sometimes in velocities in meters per second sounds very fast but if you're moving while printing there's a time of flight where you need to trigger the dispense waveform to the pzo Head well before the location you want to land on and if you're doing bidirectional printing then if you want to print on the same spot spot every time when you're going in reverse you have to figure on the opposite side of the Target location again establishing with the flight times is best done with Machine Vision print a test pattern while on the fly at a known velocity knowing where the trigger was made you can then examine the location of the deposition and determine what the flight time was for that droplet other things to look out for when using really small pazo printing there's an interesting effect when you generate a droplet from a print head it tends to pull charge with it so as that droplet five flies to the substrate you're effectively moving charge from the print head to the substrate generally not a problem but some fluids require to be dispensed in a dry environment so you need the environmentally control and dry environments are really bad for bleeding off charge so it is the case that without proper design considerations as you print charge builds up on an on an insulative substrate and that charge can deflect f future droplets as you try to print them it'll be deflected using good grounding techniques using static dispa materials and using ionizers in your environment in your enclosed environment can greatly help with accuracy because you're not having those static based influences inspection lighting once again we talked about that a little bit for droplets on a flat substrate coaxial lighting is ideal the flat substrate retroflex light straight to the camera so it looks like a white background the droplet typically domed scatters light in many directions so it looks looks very dark on the substrate the high contrast Imaging makes image processing very easy you don't have to worry about things where it can't quite tell where the edge of the droplet is it's very precise and I guess last is depending on the substance you're emitting you may need to perform these operations in a dry environment of extremely small droplets that are that contain volatiles will evaporate extremely fast so that may or may not be a problem for the process that you have but it's a consideration also temperature dependencies of materials sometimes printing masking materials their their viscosity changes rapidly with temperature so it's important to temperature control the supply lines and the print head at the proper temperature so you get a viscosity that's matched to the waveform of the pazo print head and last for certain low viscosity fluids they will tend to drool from pazo print with very low viscosity they'll form a big droplet on the print head and so you need to apply back pressure so that they set right at the right location on the print head but the head of the crint reservoir will affects the back pressure so a full tank has a certain amount of pressure on the head and if you set your back pressure so that it's proper there it may not be proper when the tank is near empty implementing active back pressure control over the reservoir to ensure sure that the pressure at the inkjet print head is consistent can greatly enhance crint quality a moving laser displacement sensor as we talked about can be moved over a component surface to generate a dispense pattern that's customed for every component and that's one of the projects we did recently that we like to talk about incoming products were their variance was large compared to the accuracy of the dispense pattern we needed to make so the solution was to 3D map the surface of the incoming product 100% and then do a dispense pattern do another 3D map so custom dispense pattern based on each product that we're working at and then with the second pass we can basically do an image subtraction and what we have left is just the dispense material and we can take that information and feed it back to the system maybe we're too thin in one area because they're moving quickly how we can slow down in that area maybe we have too much material on a corner we need to speed up there and so as incoming materials change the system can automatically adapt another piece is maintainability almost all dispense systems require maintenance you need to change out the dispense needle you need to change out the augers periodically because the material is sets up you need to clean the print head when you build a system just having a printer and just being able to print correctly is part of it being but being able to maintain that quickly and easily is also important for up time if you want a high OE you need to be able to go in perform maintenance add new material and get back to running um so some of the ways that Vision enables that is for instance automated needle tip location you take a lure lock needle out uh pressure time dispenser put a new one in the tip's no longer in the same place that it was so being able to pull that in front of a camera snap a couple images establish its new XY location makes that quick and easy to deal with automatic wiping of print heads and needles and Paso nozzles is also one technique and with that i' turn it back over to Ryan all thanks Jerry application development integrating this all together now that's what we do at AC and the thing that we want to really point out is from an end to end standpoint whether it's your product development or it's your automation or maybe it's your testing we've worked with a lot of different Technologies within our company to solve customers challenges and really taking those different Technologies and integrating them together to solve your problem is what we're here for I want to touch a little bit on design for manufacturability that's one thing that Jerry mentioned and it's really important in a lot of different applications that it's considered right up front because it can really help Drive what technology you are looking to use in your product and for the manufacturing side of things and it can be really key to your success from a cost standpoint and from a speed standpoint to get it right right away and we have a product development group that can help on those side of things and when they understand the risks typically at that point of the project they understand what to look for from a dispensing side of things and even from molding that sort of thing they can guide you in different types of adhesives different types of features to put into your part parts and really set you up for Success from the onset in your product about the life cycle I'll let Jerry touch on this next one here solving complex Precision motion challenges the appropriate technology for a given dispensing application varies depending on what you're trying to accomplish in some cases a simple pneumatic actuator is sufficient to put down a single droplet of adhesive it's simple and easy in other cases you need to dispense along the line or maybe around a circle in those cases perhaps stacked linear actual uors they're really nice for precise dispensing over XY and Z varying dispense locations and in some cases you might want to look at as at a robot almost all modern robots have excellent software that allow you do path tracing for dispensing on large work envelope objects potentially meters across but for very high accuracy systems sometimes we have resorted to using hexapod robots they give us Sixaxis control they allow us to keep critical components orthogonal to the dispense tip when we're using low viscosity components that that might otherwise want to run away from us if we were using a dispense tip to dispense around the side of a product we can keep the dispense surface always normal to the dispense tip they're extremely accurate and they're very stiff again dispensing applications are highly variable on what sort of motion you might use so picking the right motion platform is a critical component this slide's a bit of a repeat from earlier but just to go back to it we're able to help our customers by helping them in the product development stage to help thement what's required in the manufacturing stage and giving them feedback per Define for manufacturability and in some cases 100% mapping of parts in order to dispense and 100% mapping of the dispense pattern gives you all the information you might need in order to have a successful product and with suitable forethought we can do dispensing in this single digit Micron range so just wrapping up what what we talked about earlier when we started out we had a client that was really looking to find out if their product was even viable and helping them develop a platform that could really test out Technologies and find the right technology and the onset to make their product successful and so sometimes that means you can find an off-the-shelf solution but often times when you're talking about some of these micro dispensing applications and very fine precise control of your dispense and curing and whatever else might be entangled with that it really requires a custom solution and custom software to pull all that together and bringing in that Vision to the adhesive side of things and helping that work together in unison is really key to the success of a project like this on on this project we were able to put down of adhesive to within plus or minus 50 microns and there was there was a bead that was about a half a millim wide so so we needed to make sure that bead wouldn't flow one way or another as it was dispensed over a complex surface so we needed to map out that surface and dispense that bead down and then also we needed to qualify that bead was placed correctly as Jerry mentioned using some of those Technologies from Vision we could actually map out the bead that was dispensed and take a negative image of that so to speak and then actually have that ribbon of material that we could verify had been placed correctly and then automated tip calibration of course is key something that we did here and then cleaning the tip that was also key and we also made it so that we could test out multiple different dispensers on this system because again at the onset you might find that it's a UV cure adhesive that works best or maybe that's you think works and then you need to switch up to a different adhesive the characteristics of that adhesive are a little different and you need to use a little different technology to dispense that other adhesive we designed a platform for the customer that we could switch out these different adhesive dispensers to really be successful out of the gate and make sure that they had their product in a place that it could be commercialized and yeah this custom software was key along with that in in in integrating all of that together thanks Ryan just to wrap up automate The Impossible at solves the world's toughest problems through a multidisciplinary engineering approach go faster by solving complex engineering challenges and parallel with your in-house team grow stronger with differentiated IP that gives your Tech driven product a competitive advantage and go beyond the limits of your imagination with novel Solutions design Innovation and accelerated development teams thank you very much
2024-03-02 14:28